Producteur de granulats pour commencer, JPS Granulats s’est très vite lancé dans la fabrication de bétons. Puis, il a monté une unité de micronisation de fillers calcaire. Enfin, il vient d’inaugurer une petite usine de production de ciments par mélange. Une première en France, qui a abouti à la modification du référentiel NF-Liants hydrauliques.
![De gauche à droite, Mélanie Perrot, directrice générale de JPS Granulats, Olivier Stocker, président, Emilie Jacotot, responsable laboratoire, et Ana Paula Laborier, responsable qualité. [©ACPresse]](https://www.acpresse.fr/wp-content/uploads/2019/05/1JPS-Granulats-MD-1024x683.jpg)
Un à un, les grains de sable tombent. Petit à petit, ils forment un cône inversé parfait. Ils sont des milliers, des millions, enfermés dans leur prison de verre, à mesurer le temps qui passe. Ce temps qu’il faut savoir maîtriser ou avec lequel il est nécessaire d’être en phase. Ni trop tôt ni trop tard. C’est là résumé toute l’histoire de JPS Granulats, dont Olivier Stocker est l’un des fondateurs, avec son frère Jean-Pierre, et avec Mélanie Perrot. « Il faut savoir arriver au bon moment et avec le bon projet. Alors les choses se font très vite », explique Olivier Stocker.
L’entreprise est née ainsi, en 2003. En Côte d’Or, à proximité des vignobles bourguignons, d’anciens terrils marbriers témoignent d’une activité industrielle passée. Personne ne s’y intéressait, bien qu’ils soient riches d’une matière première valorisable. « Nous avons demandé et obtenu en moins d’un an l’autorisation préfectorale d’exploiter deux de ces terrils et ainsi proposer un substitut aux granulats alluvionnaires. » Une première en Bourgogne. JPS Granulats a utilisé le contexte du moment : l’aspect environnemental de son entreprise pour obtenir l’impossible. Ainsi, le Terril de Villers-la-Faye, d’un volume de 250 000 m3 a permis d’obtenir 500 000 t de granulats, valorisés à 100 % sur des chantiers de travaux publics, ligne TGV en tête. Ceci, alors même qu’il se situait sur un secteur classé Unesco… Le Terril de Prémeaux-Prissey a connu un destin similaire, disparaissant du paysage du même coup. Les buttes ont laissé place à des sentiers, serpentant au milieu de sites réaménagés.
Remplacer l’alluvionnaire par le concassé
![JPS Granulats a mis en place son laboratoire de contrôles et d’essais sur ses matières premières et su sa production. [©ACPresse]](https://www.acpresse.fr/wp-content/uploads/2019/05/2JPS-Granulats-MD-1024x683.jpg)
En parallèle, JPS Granulats décroche l’autorisation d’exploiter une carrière de roche massive calcaire, à cheval sur les communes de Villers-la-Faye et de Chaux. Aujourd’hui, le groupe est à la tête de dix carrières et de deux plates-formes de stockage. « Cinq de nos carrières sont exploitées en permanence et trois, de manière occasionnelle, en fonction des besoins. »Assez naturellement, le BPE s’est invité dans l’organigramme du groupe. « Cette activité constitue un bon débouché pour une partie de notre production de granulats. Nous sommes dans une synergie de groupe et dans l’intégration verticale », reprend Olivier Stocker. Ainsi, en 2008, JPS Granulats devient le premier industriel bourguignon du BPE à substituer 100 % des granulats alluvionnaires présents dans ses bétons par des matériaux issus du concassage. Et ceci, dans le cadre du chantier de l’hôpital de Chalon-sur-Saône (71), pour lequel il a fourni 36 000 m3de béton.
L’activité BPE a suivi la même courbe ascendante que celle des carrières. JPS Granulats a installé quatre centrales fixes et trois mobiles, qu’il propose aux chantiers de sa zone de chalandise. Et comme pour les carrières, l’industriel a opté pour des équipements d’occasion (Frumecar, Imer, Pataud, Teka) qu’il a entièrement reconditionnés et adaptés à ses besoins. A l’image des skips, remplacés par des convoyeurs, qui vident les granulats dans une trémie d’attente placée au-dessus des malaxeurs. « A l’usage, j’estime que le skip est un équipement contre-nature dans une centrale à béton… »
Valoriser les matières premières
![Bâtiment abritant l’usine de micronisation. Au centre de l’image, juste derrière le silo se cache le local où se concentre l’unité de production du ciment. [©ACPresse]](https://www.acpresse.fr/wp-content/uploads/2019/05/3JPS-Granulats-MD-1024x683.jpg)
Toujours dans la logique d’une stratégie d’intégration verticale et de développement durable, JPS Granulats a monté une usine de micronisation où sont élaborés des fillers calcaire. L’idée était de valoriser au maximum les matières premières extraites des carrières. « Nous disposons de matériaux de qualité et il semblait intéressant d’en micromiser une part. »Installée sur le site de Villers-la-Faye, l’usine produit trois qualités de fillers : un 0/63 µm, un 100/500 µm et un 500/1500 µm. Les usages en sont multiples et classiques. « La production se répartit entre l’amendement, c’est-à-dire la fertilisation des sols, le nutriment minéral animalier, la production d’enrobés et celle de bétons », explique Olivier Stocker. Mais ce ne sont plus les seuls usages, puisque JPS Granulats vient de franchir une nouvelle étape dans son développement. « Nous lançons notre propre ciment ! »Toutefois, le timing, ici, a été un peu plus long…
Le postulat de départ était toujours le même : le contexte environnemental. « Nous avions le souhait d’utiliser un ciment moins riche en clinker, moins émetteur de CO2. Et avec notre usine de micronisation de fillers, nous avions les moyens de le faire. »Pour autant, créer une usine cimentière ne fut pas une promenade de santé. « Notre objectif premier était de développer un produit en phase avec la normalisation », souligne Emilie Jacotot, responsable du laboratoire.
Et maintenant, le ciment
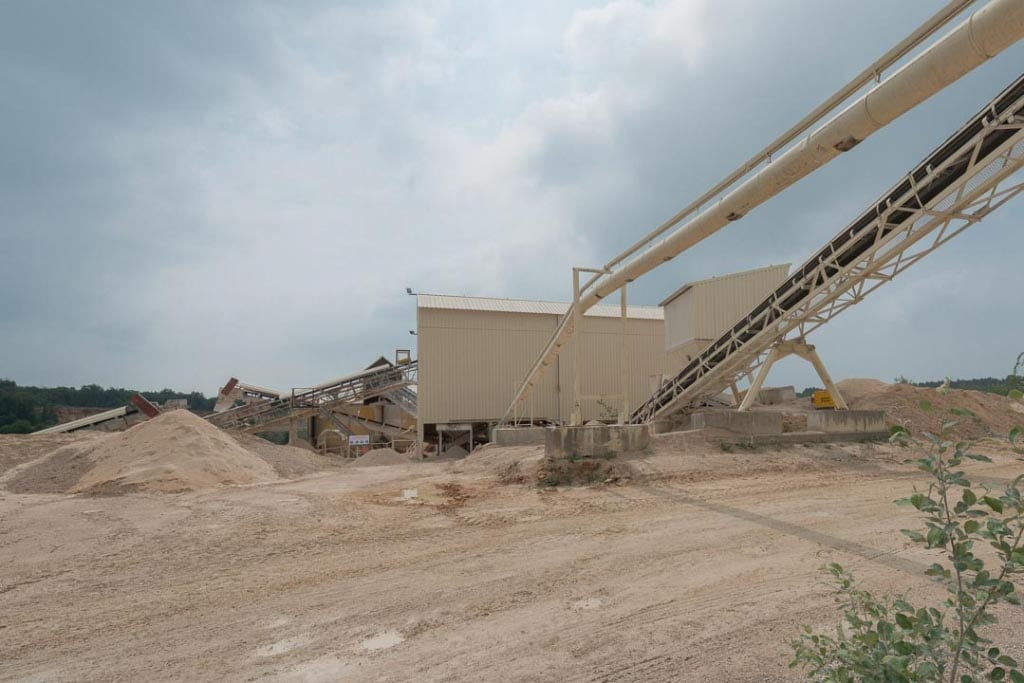
Et là, un problème de taille est apparu : le référentiel NF – Liants hydrauliques (NF 002) n’autorise pas les mêmes choses que le référentiel CE Ciments (CE 002) ! En France, selon la NF, pour être producteur de ciment, il faut soit fabriquer le clinker de base, soit, a minima, avoir un broyer sur son site. De son côté, la CE reconnaît une troisième voie cimentaire : la possibilité de mélanger des poudres venant de l’extérieur. Qu’à cela ne tienne, JPS Granulats a soulevé le problème et réussi à faire modifier – disons, à mettre à jour – le référentiel NF, à présent en phase avec le référentiel CE [lire encadré]. Le groupe bourguignon a ainsi ouvert une voie, dans laquelle d’autres industriels ne vont sans doute pas tarder à s’engouffrer. A commencer par Ecocem qui, son site de Dunkerque (59) tout juste inauguré, prévoit la production de ciments CEM III, par mélange.
La nouvelle unité de production cimentaire de JPS Granulats jouxte l’usine de micronisation. Elle assure la fabrication d’un CEM II/B-LL 42,5 N CE sur la base d’un CEM I 52,5 acheté sur le marché européen, mélangé au filler calcaire maison. « Notre ciment présente une teneur de l’ordre de 75 % de CEM I et de 25 % de filler calcaire d’une fine 0/63 µm », précise Ana Paula Laborier, responsable qualité du groupe.
Récompense bien méritée
![La production de ciments et de fillers calcaire est stockée dans les silos. [©ACPresse]](https://www.acpresse.fr/wp-content/uploads/2019/05/5JPS-Granulats-MD.jpg)
Les matières premières (ciment et filler, d’une densité comparable) sont introduites dans le mélangeur à l’aide d’une vis d’Archimède. De type horizontal, le mélangeur est un équipement neuf, mais il a été modifié en interne pour répondre de manière précise aux attentes de l’industriel. Les matériaux y séjournent 2 mn environ, avant d’être évacués vers leur silo de stockage final. Pour le moment, le ciment est proposé en vrac, mais la construction d’une ligne d’ensachage est déjà programmée. Elle devrait être opérationnelle d’ici la fin de l’année. La mise en service de l’usine cimentière a aussi été l’occasion de créer une nouvelle marque au sein du groupe JPS Granulats : Ciments 2170. “21”, comme le département de la Côte-d’Or et “70”, comme la Haute-Saône. Simple et efficace.
L’activité cimentière de JPS constitue l’aboutissement de près de quatre années de travail de l’équipe R&D composée par Emilie Jacotot et Ana Paula Laborier. Et dont l’obtention de la certification NF-Liants hydrauliques, en février 2018, est la récompense bien méritée. Pour autant, Ciments 2170 ne compte pas s’arrêter en si bon chemin. « Nous sommes en train d’homologuer un CEM II de type 32,5. Ce ciment sera proposé à la vente en sacs », dévoile Ana Paula Laborier.
Reproduire le modèle
![JPS Granulats réfléchit à la possibilité de licencier son process industriel de production de ciments. [©ACPresse]](https://www.acpresse.fr/wp-content/uploads/2019/05/6JPS-Granulats-MD-1024x683.jpg)
Plus tard, ce sont des ciments ternaires, qui pourraient sortir de l’usine. « Notre outil de production offre la possibilité d’intégrer un troisième constituant », souligne Emilie Jacotot. Ne reste plus qu’à attendre la publication à l’échelle européenne de la nouvelle version de la norme ciment NF EN 197-1. Celle-ci prévoit, en particulier, la création d’une classe C dans la famille des CEM II et la naissance de la famille des CEM VI. Ce qui correspond aux ciments ternaires.
![JPS Granulats produit trois qualités de fillers calcaire : un 0/63 µm, un 100/500 µm et un 500/1500 µm. [©ACPresse]](https://www.acpresse.fr/wp-content/uploads/2019/05/8JPS-Granulats-MD.jpg)
Enfin, avec une capacité de production annoncée de 30 000 t/an, Ciments 2170 offre une alternative cimentière pour les utilisateurs de la zone de chalandise, qui reste limitée à un rayon d’environ 200 km autour de l’usine. Et au-delà ? « Nous réfléchissons à la possibilité de licencier notre process industriel. Il est opérationnel. La mise au point des ciments a été faite. Et le contexte normatif ne pose plus de problème », conclut Olivier Stocker. Tout est donc en place pour reproduire le modèle ailleurs, pour un investissement très inférieur à une cimenterie ou une station de broyage. Une nouvelle ère cimentière est-elle en train de débuter ?
Enfin, avec une capacité de production annoncée de 30 000 t/an, Ciments 2170 offre une alternative cimentière pour les utilisateurs de la zone de chalandise, qui reste limitée à un rayon d’environ 200 km autour de l’usine. Et au-delà ? « Nous réfléchissons à la possibilité de licencier notre process industriel. Il est opérationnel. La mise au point des ciments a été faite. Et le contexte normatif ne pose plus de problème », conclut Olivier Stocker. Tout est donc en place pour reproduire le modèle ailleurs, pour un investissement très inférieur à une cimenterie ou une station de broyage. Une nouvelle ère cimentière est-elle en train de débuter ?
Frédéric Gluzicki
Un problème de référentiel résolu…
Dans le document intitulé “Modalités d’application du marquage CE Ciments”, identifié CE 002 et mis en application le 1erjuillet 2013, il est fait mention de différentes catégories de cimenterie. Ceci au niveau de l’Annexe 4. Ainsi, trois types sont distingués :
- les cimenteries traditionnelles où le clinker et le ciment sont produits sur le même site ;
- les usines de broyage où le ciment est produit par broyage de clinkers, provenant d'autres sites et d'autres constituants ;
- les usines de mélange où les constituants du ciment sont reçus broyés, ceux-ci pouvant être reçus déjà combinés comme ciment, et ensuite mélangés pour produire un ciment fini.
En revanche, le référentiel de certification NF Liants hydrauliques, identifié NF 002, toujours du 1erjuillet 2013, n’indiquait pas la même chose. Dès la première page du document, il était précisé que : “Une usine est, au sens du référentiel de certification de la marque NF Liants hydrauliques, une installation utilisée pour la production de ciment dans laquelle le clinker est broyé sur le site de fabrication du ciment […].”
Le nouveau NF 002
En comparant les deux définitions, celle du marquage CE et celle de la marque NF, on voit qu’il y a comme un petit problème, car ce que permet le premier texte, n’est pas autorisé par le second… Mais ça, c’était avant. Et depuis le 2 mai 2017, les choses sont rentrées dans l’ordre. Ainsi, le nouveau référentiel de certification NF Liants hydrauliques, toujours identifié NF 002, distingue à présent, trois catégories d’usine :
- les usines de ciment complètes traditionnelles dans lesquelles le clinker et le ciment sont produits sur le même site ;
- les usines de broyage, dans lesquelles le ciment est produit par broyage de clinker et d’autres constituants approvisionnés ;
- les usines de mélange dans lesquelles le ciment est produit par mélange de clinker préalablement broyé à l’extérieur du site, reçu en tant que CEM I, bénéficiant d’un certificat de constance de performances et d’autres constituants.