L’ajout au processus de production du béton d’un système de contrôle et de mesure de l’humidité représente une solution simple et rentable. Le béton ainsi obtenu sera constant d’une gâchée à l’autre, améliorant la qualité du produit et réduisant le gaspillage, ainsi que les déchets. Explications.
![Test d’affaissement (slump) d’un béton. [©Hydronix]](https://www.acpresse.fr/wp-content/uploads/Hydronix-1024x683.jpg)
La consommation mondiale de béton avoisine 1 t/personne/an, ce qui en fait le deuxième matériau le plus consommé après l’eau. Le béton contient au minimum trois éléments : granulats (gravier et sable), liants (ciment) et eau. Une fois combinés, ces éléments créent une réaction chimique, qui permet au béton de durcir. Toutefois, le contrôle de l’humidité constitue une partie fondamentale du processus de fabrication. La personne qui produit le béton, effectue un test d’affaissement (slump). Afin de vérifier la maniabilité, la fluidité et la consistance du mélange. Divers facteurs affectent les résultats du test d’affaissement : la quantité de granulats, d’adjuvants ou encore la teneur en eau.
I – Pourquoi le contrôle est-il important ?
Idéalement, les granulats et le ciment seraient complètement secs et la quantité d’eau nécessaire pour chaque gâchée se résumerait à un volume fixe, assurant la production d’un béton de qualité constante d’une gâchée à l’autre. Dans la réalité, les granulats sont stockés en tas, parfois en plein air. Leur teneur en humidité change en permanence, en raison des effets inévitables de la décantation.
Dans les centrales à béton actuelles, on pèse les matériaux, en fonction d’une formule. Avec, comme objectif, le poids “sec” présumé de chacun de ces matériaux. Néanmoins, les granulats pesés contiennent une quantité inconnue d’eau. Ce surplus d’eau aura des répercussions importantes sur les ratios eau/ciment, granulats/ciments. Mais aussi sur la plasticité ou la couleur du mélange. Sa non-prise en compte entraînerait des irrégularités au niveau de l’affaissement, de la résistance, de la couleur, générant un produit final de piètre qualité.
![Décantation naturelle de l’humidité dans un tas de granulats. [©Hydronix]](https://www.acpresse.fr/wp-content/uploads/2-Hydronix-Granulats-1024x504.jpg)
II – Pourquoi le bon calcul est-il essentiel ?
En imaginant que la fabrication d’un béton respecte une recette basée sur des quantités fixes de granulats et de ciment et sur un simple ajout d’une quantité d’eau programmée, chaque gâchée produite n’en reste pas moins différente, à cause de la teneur en eau inconnue et variable des granulats. Par exemple, si une recette demande 1 t de granulats, à moins qu’ils ne soient absolument secs, la quantité pesée ne représentera pas 1 t de granulats, mais plutôt 1 t d’un mélange de granulats et d’eau.
Pour déterminer le degré d’humidité exact d’un granulat, il faut prélever un échantillon du granulat. Puis, le peser, le sécher pour en évaporer l’eau et le repeser. La manipulation est répétée autant de fois que nécessaire pour que le poids ne bouge plus (ce qui signifie que l’échantillon est complètement sec). On peut ainsi rectifier la valeur pesée pour obtenir la valeur correcte de granulats secs définie dans la recette. On peut le calculer ainsi :
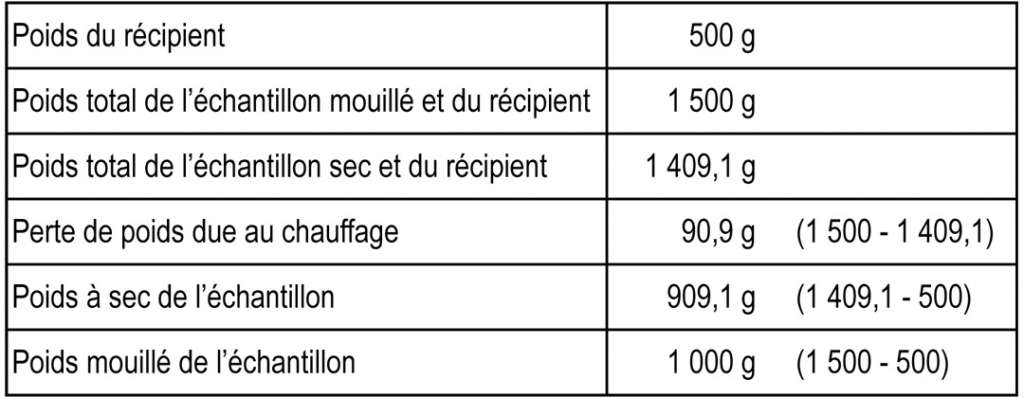
Ces valeurs peuvent être utilisées pour calculer le pourcentage d’eau dans le matériau, comme suit :

Les mêmes valeurs utilisées pour une humidité à base mouillée produiraient les résultats suivants :

On comprend l’importance d’utiliser la même méthode de mesure tout au long des calculs de l’humidité.
L’avantage de travailler avec la méthode “humidité base sèche” est de simplifier les calculs pour définir le poids à atteindre à partir du poids initial.
III – Comment les changements d’humidité affectent-ils les proportions de matériaux ?
Les exemples suivants montrent l’effet de variation d’humidité des granulats sur les dosages des matériaux. En effet, de même que la valeur d’humidité, la proportion de chaque matériau dans le mélange s’avère un facteur clef pour déterminer l’affaissement du béton.
Si une gâchée pesée contient du sable à 10 % d’humidité et des graviers à 0 %, on obtiendra un ratio des matériaux suivant :
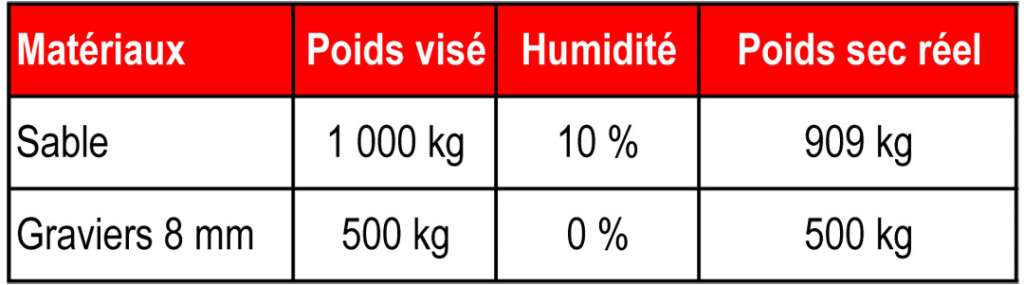
Le ratio sable/graviers est alors de 1,8 : 1
Toutefois, pour une autre gâchée, si le sable est à 0 % d’humidité et les graviers à 5 %, on aura :
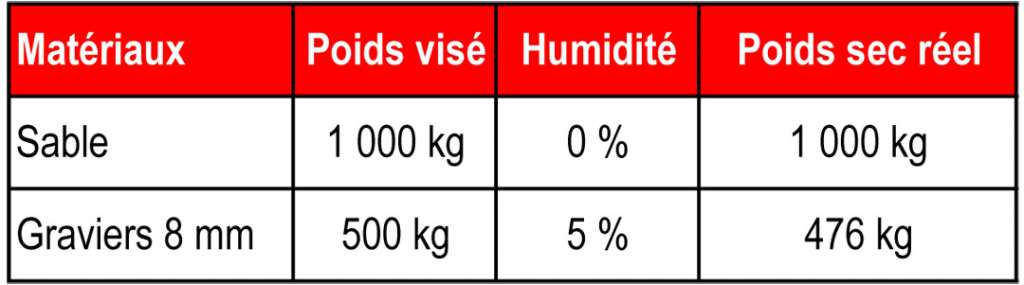
Le ratio sable/graviers devient 2,1 : 1.
Cela occasionne une différence importante de ce ratio d’une gâchée à l’autre. Et sans correction, cela aura un impact direct sur la qualité du béton produite. Il est donc indispensable que la teneur en eau des granulats soit mesurée avec précision, afin de compenser et d’incorporer au mélange l’équivalent du poids sec de chaque matériau.
Dans l’absolu, l’eau à ajouter pour finaliser le mélange peut être calculée selon la teneur en humidité des granulats, permettant ainsi l’obtention d’un ratio eau/ciment correct et d’un slump uniforme. Mais pour une performance optimale, il sera judicieux de contrôler l’humidité du mélange – par exemple à l’aide d’une sonde micro-ondes placée dans le malaxeur – pour permettre un ajout d’eau en conséquence.
IV – Quelles sont les problèmes associés aux variations d’humidité ?
Si, pour un mélange de béton, on ne respecte pas les proportions des matériaux ou que le taux d’humidité est incorrect, on aura des problèmes de consistance, de maniabilité et d’affaissement du béton.
Il paraît évident d’en tenir compte en BPE, qui doit livrer à ses clients un béton d’une consistance et d’une résistance contractuelles, chose qui sera susceptible d’être vérifiée par un test d’affaissement au moment de la livraison.
Même nécessité en préfabrication, car des variations d’humidité pourront causer des problèmes de séchage et de décoffrage. Par exemple, les tuyaux pourront s’effondrer au démoulage ou les blocs se désagrégeront en sortie de presse. Les dalles alvéolées y sont aussi très sensibles, avec des risques d’affaissement ou de déformation au fur et à mesure de la progression de la machine à coffrage glissant sur la ligne de production.
Une variation d’humidité occasionnera une modification de la surface apparente des granulats. Ceci peut revêtir une grande importance lors de l’ajout de colorants dans une gâchée de béton. En effet, la couche de pigment en surface variera en fonction des proportions du mélange. Ceci entraînera des différences de couleur.
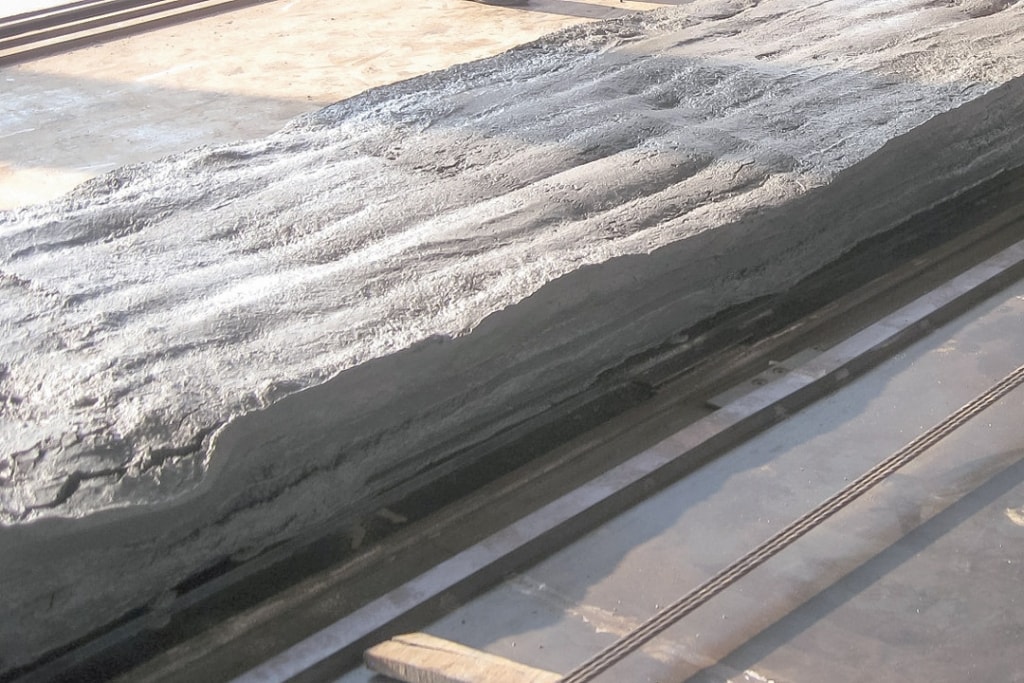
V – Quelle méthode de mesure de l’humidité doit-on utiliser ?
Même si les résultats par séchage en laboratoire peuvent être précis, les manipulations sont chronophages et ce principe ne permet pas de modifier les dosages de matériaux en temps réel. Il existe plusieurs méthodes de mesure de l’humidité : méthodes capacitive ou résistive, par infrarouges ou par micro-ondes. Chacune peut être utilisée pour automatiser le processus et possède ses propres avantages et inconvénients. L’un des systèmes les plus populaires fait appel aux sondes micro-ondes. Certains modèles utilisent même une technique numérique de mesure, ce qui permet de ne pas être affecté par les impuretés, la couleur, la taille des particules ou la température. On pourra ainsi obtenir une précision de +/- 0,2 %.
Samuel Masson, Appui technique et ventes France d’Hydronix