La valorisation et le traitement en centrale des retours de bétons frais se sont généralisés, prenant en compte les problématiques de l’économie circulaire, qui intéresse le secteur de la construction. Les dispositifs de lavage ou les bennes de durcissement permettent de donner une seconde vie à des bétons qui, autrefois, étaient considérés comme des déchets encombrants.
Retrouvez cet article dans le n° 948 de Process Industriels , supplément de Béton[s] le Magazine n° 87
![Les excédents de béton non utilisés et retournés en centrale ne sont donc pas à prendre à la légère. Benne de recyclage sur le site Celtys de Landivisiau (29). [©ACPresse]](https://www.acpresse.fr/wp-content/uploads/2020/10/1-Recyclage-Couverture.jpg)
Les déchets béton de l’activité du BTP représentent 3 à 4 % de la production de béton en France, soit le volume annuel en granulats de quatre grosses carrières ! Les excédents de béton non utilisés et retournés en centrale ne sont donc pas à prendre à la légère. Alors que la filière béton fait sa mue pour économiser la ressource et baisser son empreinte carbone. Les matériaux doivent participer à l’effort global pour parvenir à un objectif, qui révèle des moyens cachés d’y parvenir. Des moyens qui ont évolué, suivant de près l’évolution même du béton.
D’un produit ferme, stable, transporté à la brouette et manipulé à la pelle, le béton est devenu une matière fluide, parfois auto-plaçante. Sa composition, avec des éléments plus fins qu’auparavant, a eu de facto une influence sur le traitement des rejets eux-mêmes. Lesquels terminaient dans des bacs de décantation. Par sédimentation, les éléments lourds étaient récupérés. Problème : l’eau claire, qui était soit repompée pour être réinjectée dans le béton, soit rejetée dans l’environnement, était chargée d’un pH élevé, de l’ordre de 12 à 13… Solution : neutraliser ce pH, en y injectant du CO2 par exemple.
Cet article est réservé aux abonnés
des revues Béton[s] le Magazine et Process Industriels.
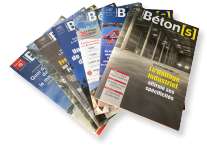
En plus de votre magazine, profitez d’un accès illimité à l’ensemble des contenus et services du site www.acpresse.fr :
- Lecture de l’intégralité des dossiers thématiques, reportages chantiers, fondamentaux, histoire de la construction…
- Consultation des indicateurs économiques (chiffres et analyses)
- + vos newsletters pour suivre l’info en continu
Lavage et recyclage des granulats
Il y a une trentaine d’années, sont apparus les premiers équipements permettant de délaver le béton et d’en séparer les éléments lourds. Des systèmes qui voient le jour alors que les bétons sont encore assez fermes, donc pauvres en éléments fins. La venue des auto-plaçants aura alors rebattu les cartes, en ayant un effet collatéral. Des eaux chargées ont demandé le développement de systèmes de filtration, comme les filtres-presses. Avec en sus la production de galettes de boue devant être évacuées. Une sorte de retour à la case départ. L’apparition de recycleuses et de bennes de durcissement aura permis de prendre en compte la problématique récurrente de la laitance lors du traitement des retours de béton frais. Et pour cause : 1 m3de béton dans la toupie, ce sont 350 kg de ciment qui ont servi à le fabriquer qui partent dans l’eau.
Bennes Béton Desgranges : Durcisseur à béton
![Bennes Béton Desgranges propose une benne de durcissement, d’une capacité de 6,5 m3. [©ACPresse]](https://www.acpresse.fr/wp-content/uploads/2020/10/2-Recyclage-Desgranges-600x400.jpg)
Bennes Béton Desgranges propose une benne de durcissement, d’une capacité de 6,5 m3.
[©ACPresse]
Bennes Béton Desgranges est un industriel de Saône-et-Loire, qui propose une benne de durcissement d’une capacité de 6,5 m3. Soit quelque 15 t de matériaux à recycler... Son système est simple et basé sur le principe du démoulage, une fois le béton durci. Un système mécanique breveté permet après 12 h de séchage minimum d’assurer le déchargement du bloc sur une plate-forme de concassage. Le transport de la benne s’effectue par camion Ampliroll standard. Simple et efficace.
Béton Stone Consulting : La solution s’appelle Ecofrog
![Le système de recyclage Ecofrog est distribué en France par Béton Stone Consulting. [©ACPresse]](https://www.acpresse.fr/wp-content/uploads/2020/10/3-Recyclage-BSC-600x400.jpg)
Le système de recyclage Ecofrog est distribué en France par Béton Stone Consulting.
[©ACPresse]
Béton Stone Consulting (BSC) propose l’Ecofrog, un système de recyclage des eaux de lavage et des restes de béton. La laveuse RE_X utilise le principe de la décantation, afin de séparer les différents éléments du béton. Elle fonctionne sur le principe de flottaison pour séparer les résidus de béton des graviers, avec une coupure à 0,25 mm, de l’eau de lavage (ciment et éléments fins restant en suspension dans l’eau). Les eaux chargées sont maintenues en suspension dans le bassin d’agitation et peuvent être pompées directement dans le malaxeur pour leur réutilisation. Les granulats sont éjectés à l’aide d’une goulotte vibrante ascendante. L’eau d’égouttage retourne dans la laveuse et l’on obtient un lavage parfait des granulats, qui peuvent ainsi être réutilisés. La gamme Ecofrog RE_X permet de traiter de 2 m3/h à 26 m3/h. « L’avantage de cette solution est qu’elle fonctionne sans vis, mais à l’aide d’un couloir vibrant dans lequel on rince le granulat avant de l’extraire de la machine une fois égoutté, explique Sylvain Adam, gérant de BSC. Les laveuses classiques à vis qui servent à extraire les gros éléments ont le désavantage de garder la laitance. Ce matériel nous permet de garantir à nos clients que les minéraux au-dessus de 0,25 mmsont dépourvus de laitance de ciment et ne risquent pas de durcir dans les trémies de stockage pour leurs réutilisations dans la production. » BSC possède aussi un certain nombre de systèmes de séparation des minéraux de l’eau pour valoriser les éléments inférieurs à 0,25 mm,dans l’objectif du zéro déchet. Notamment la tour de décantation Aquare_X et le filtre-presse RE_Xpress.
Bibko : Comtec en circuit ouvert ou fermé
![Le système Comtec de Bibko peut fonctionner en circuit ouvert ou fermé. [©ACPresse]](https://www.acpresse.fr/wp-content/uploads/2020/10/4-Recyclage-Bibko-600x400.jpg)
Le système Comtec de Bibko peut fonctionner en circuit ouvert ou fermé.
[©ACPresse]
Le système Comtec de Bibko, spécialiste allemand du recyclage de béton résiduel, peut fonctionner selon deux modes distincts. La première solution consiste à récupérer les composants contenus dans le béton résiduel pour les réutiliser dans le malaxeur de la centrale à béton. Par contre, les particules fines collectées dans le bassin de sédimentation sont récupérées pour être mises en décharge. Cette solution fonctionne donc en circuit ouvert. La seconde approche permet de faire fonctionner le dispositif en boucle fermée. Ici, en plus de la récupération des résidus de sable et de graviers contenus dans le béton, l’eau résiduelle chargée en fines peut être réinjectée dans le processus de production. Cela permet de garantir une circulation continue tout en maintenant l'équilibre hydrique le plus constant possible. Cette approche ne produit pas de perte de matières premières, ni d’eau.
Cembox : La benne est son métier
![La benne Cembox est conçue pour réceptionner les retours de béton, de mortiers et même de chapes fluides. [©Cembox]](https://www.acpresse.fr/wp-content/uploads/2020/10/5-Recyclage-Cembox-600x400.jpg)
La benne Cembox est conçue pour réceptionner les retours de béton, de mortiers et même de chapes fluides.
[©Cembox]
L’un des leaders du marché, la société Cembox basée près de Nantes, a lancé, il y a une dizaine d’années, son concept de bennes étanches, dont le principe consiste à récupérer les excédents de béton, à les faire durcir, puis à les concasser. Avantage : limiter le problème des eaux chargées. « La particularité de la benne Cembox est sa forme très évasée, qui permet au bloc de descendre très rapidement en raison de l’absence d’angles rentrants, résume Daniel Lebréquier, président de l’entreprise. J’ai finalement créé non pas une benne, mais une sorte de moule qui se vidange de manière aisée, en l’inclinant grâce à un système de palonnier mécanique situé à l’intérieur de la benne, qui permet de décoller le béton durci. » La Cembox est conçue pour réceptionner les retours de béton, les mortiers auto-plaçants, mais aussi les résidus chapes anhydrite. La gamme de bennes permet de faire des blocs de 12, de 15 ou de 25 t. « La particularité de ces blocs récupérés est de constituer un gisement de qualité, car ce n’est au final que du béton, poursuit Daniel Lebréquier, qui possède quelque 600 bennes en activité en France. C’est un matériau très recherché de nos jours par les bétonniers pour développer leur gamme d'éco-granulats, dans la démarche de l’économie circulaire. »La benne Cembox n’est d’ailleurs plus seulement une affaire de bétonnier, c’est devenu une affaire de chantier. Quelque 80 % des centrales de Bretagne et des Pays de Loire sont désormais pourvues de bennes aujourd’hui, et de plus en plus de chantiers s’équipent aussi pour remplacer leurs bennes à gravats. Et ainsi engager la traçabilité de leurs rejets.
Imer : L’affaire est dans le big bag
![L’Ecod’O Soft d’Imer est destinée aux chantiers pour traiter les restes de béton des centrales mobiles [©Imer]](https://www.acpresse.fr/wp-content/uploads/2020/10/6-Recyclage-Imer-600x400.jpg)
L’Ecod’O Soft d’Imer est destinée aux chantiers pour traiter les restes de béton des centrales mobiles
[©Imer]
L’eau, c’est également ce dont il est question chez Imer qui, grâce à son système Ecod’O, assure une récupération des inertes et des résidus de laitance, avec un principe de récupération unique. La solution est basée sur un bac receveur couplé à un big bag filtrant posé au sol. Le premier élément va récupérer les eaux de lavage, qui ont servi au nettoyage des différents matériels servant à la production du béton. Ceux-sont sont acheminés vers le big bag, qui va engager le processus de décantation et de déshuilage. Une station va ensuite permettre de rééquilibrer le pH pour un rejet aux eaux pluviales grâce à un traitement au CO2. Si la station de lavage Ecod’O est plutôt recommandée sur les sites de préfabrication, sa petite sœur Ecod’O Soft est, quant à elle, destinée aux chantiers pour traiter les restes de béton des centrales mobiles, ainsi que les résidus de lavages des livraisons BPE par camion-toupie. Le secret du système réside dans la pompe à crépine, qui vient récupérer la laitance pour l’acheminer vers le big bag dans lequel est retenu le tout-venant. « Nous avons conçu une machine mobile et compacte, qui permet tout à la fois de récupérer la laitance, les eaux de lavage, les granulats pour, d’un côté, recycler et, de l’autre, réutiliser, argumente William Merger, directeur de division chez Imer France. Ce matériel ne vient pas presser les boues comme dans un filtre-presse, mais agit par décantation de l’eau, pour soit la réutiliser pour le lavage des outils de production du béton, soit pouvoir la rejeter dans le réseau d’eaux pluviales après traitement. Il peut venir en appui ou indépendamment d’installations existantes de lavage ou de bacs de décantation. » Ecod’O peut traiter en moyenne 2 m3/h de recyclés.
Liebherr Malaxage et Techniques : A vis ou à cuve
![Système de recyclage à cuve de type LRT signé Liebherr Malaxage et Techniques. [©Liebherr]](https://www.acpresse.fr/wp-content/uploads/2020/10/7-Recyclage-Liebherr-600x400.jpg)
Système de recyclage à cuve de type LRT signé Liebherr Malaxage et Techniques.
[©Liebherr]
Liebherr a développé deux solutions de traitement des retours de béton frais. La première dite “à vis” joue sur la compacité, tandis que la seconde, à cuve, est adaptée au recyclage des mortiers. Un remplissage en sable très fin permet de véhiculer les retours de béton en hauteur, lesquels sont asséchés dans la montée de la vis. Les produits ressortent à plus de 2 m de hauteur, sous la forme d’un mélange de sable et de graviers. Les éléments inférieurs à 0,25 mm passent en surverse dans un bassin agité en permanence de manière à éviter la décantation. Le tout fonctionne en circuit fermé, repris par des pompes à eaux chargées dans le bassin des résidus de fines de ciment. Ce système comprend trois tailles : LRS 606, LRS 708 et LRS 806. La première installation est destinée à des centrales à béton de petite capacité avec une cadence de 12 m3/h. La 2eparvient à traiter 22 m3/h. Enfin, la plus imposante peut être mise en fosse, le niveau 0 par rapport à la trémie de réception facilitant l’accès des bétonnières pompes. D’un débit d’environ 20 m3/h, le système à cuve LRT est formé de pales, qui brassent le béton de manière à soulever les particules fines de ciment et de sable qui restent en suspension. Ceci garantit la séparation d’avec les éléments plus lourds. La cuve de recyclage présente un diamètre de 2,40 m avec une rotation identique au système à vis.« Le système à cuve tourne beaucoup plus lentement avec une cadence d’à peine 6 tr/mn,précise Antoine Jentner, chargé d’affaires centrales à béton et recyclage chez Liebherr Malaxage et Techniques.Cela permet par exemple, lors des retours de mortiers, d’assurer une sédimentation plus importante. L’auge de réception de 4 m de large avec 2 cannes parallèles permet aussi une capacité de recyclage de volumes plus importants. En effet, 2 toupies peuvent déverser en même temps jusqu’à 2 m3instantanément dans la cuve de recyclage. Alors qu’avec la vis d’Archimède, ce processus est plus lent. » Enfin, il est possible de coupler une auge de réception avec un système à vis.
Schwing Stetter : Granulats récupérés à 100 %
![Schwing Stetter développe depuis les années 1980 une centrale de recyclage, qui se décline en trois capacités de traitement. [©Schwing Stetter]](https://www.acpresse.fr/wp-content/uploads/2020/10/8-Recyclage-Schwing-Stetter-600x400.jpg)
Schwing Stetter développe depuis les années 1980 une centrale de recyclage, qui se décline en trois capacités de traitement.
[©Schwing Stetter]
La solution développée par Schwing Stetter, lancée dès les années 1980, consiste en une centrale de recyclage, proposée en trois formats : RA 6, RA 12 et RA 20. Les capacités de traitement du béton résiduel oscillent respectivement entre 6 et 20 m³ /h. Si le concept s’est amélioré de manière progressive avec les avancées technologiques et la modification de la composition des bétons, le principe de fonctionnement demeure identique. Il s’agit de défaire le béton, en le lavant grâce à un tambour posé sur galets et qui tourne sur lui-même. Une ligne d’eau va laver selon le principe de contre-courant le granulat au fur et à mesure de son parcours dans le tambour. Et ce, jusqu’en sortie. Le gravillon de grain supérieur à 0,2 mm est extrait de la cuve de lavage à travers un sillon vibrant, l’emploi d’un tamis assurant l’assèchement des gravillons. Les eaux contenant des composants, dont le grain est inférieur à 0,2 mm sont brassées par un mélangeur, afin d’éviter le dépôt des particules fines et permettre ainsi de les réinjecter dans le processus de fabrication du béton. Ce qui permet de limiter les rejets dans les bacs de décantation. « Nos machines permettent de récupérer 100 % du granulat issu du béton résiduel,explique Thomas Besnard, ingénieur commercial pompes à piston industrielles et centrales à béton chez Schwing Stetter. Ce granulat est en tous points identique en qualité à celui qui est utilisé au départ pour fabriquer du béton, hormis le fait qu’il a été débarrassé de ses fines. En sortie de tambour, ce granulat qui n’est plus normé est prêt pour être vendu comme du tout-venant ou du pré-mélange, en fonction du profil des utilisateurs des centrales à béton. »
Stimm : Silo à boue et benne de durcissement et de lavage
![Silo à boue signée Stimm. [©Stimm]](https://www.acpresse.fr/wp-content/uploads/2020/10/9-Recyclage-Stimm-600x400.jpg)
Silo à boue signée Stimm.
[©Stimm]
Le silo à boue de Stimm est conçu pour séparer les boues de l’eau lors du process de traitement des retours béton. Dans un bassin agité, les eaux chargées sont pompées dans le silo. L’eau se décante de manière naturelle, les matériaux les plus lourds se déposant au fond du silo par gravité. Lorsque l’eau chargée atteint une certaine densité, des boues pelletables sont obtenues par le biais d’un filtre. Un système de doubles vannes guillotines permet d'évacuer les boues, qui sont collectées sous le silo. L’eau claire est alors renvoyée dans un bassin d’eau décantée. Par ailleurs, Stimm propose aussi une benne de retour béton et une benne de lavage.
Wam : Plutôt orienté préfabrication
![Le séparateur à béton Consep 5000 est développé par l’industriel italien Wam. [©ACPresse]](https://www.acpresse.fr/wp-content/uploads/2020/10/10-Recyclage-Wam-600x400.jpg)
Le séparateur à béton Consep 5000 est développé par l’industriel italien Wam.
[©ACPresse]
Pour sa part, l’Italien Wam a développé le séparateur à béton Consep 5000. En clair, une recycleuse capable de traiter des retours de béton en quantité assez importante, y compris des toupies pleines. Lancé en 2013, cet équipement est aussi destiné aux installations de béton préfabriqué. Le principe rejoint celui utilisé dans la valorisation des bétons résiduels. D’un côté, traiter le sable et les graviers. Et de l’autre, l’eau chargée grâce à un recyclage par vis. Le séparateur est composé d'une auge en forme de “U” et d’une trémie avec une grande bouche de chargement, les deux revêtues en polymère technique résistant à l’usure. Sa capacité de traitement est de 20 m³ en béton dilué avec de l’eau ajoutée. Un séparateur à vis vient ensuite remonter l’ensemble des granulats, l’eau chargée repartant vers des bassins de décantation. « La vis qui sert à remonter les granulats et l’eau est formée de matériaux synthétiques de type polymères. Ce qui évite que le béton ne colle dessus, tout en augmentant la résistance à l’abrasion,précise Serge Angelosanto, directeur général de Wam France. Mais le grand avantage de ce séparateur est qu’il est moins gourmand en énergie, et en eau, puisque celle-ci sert à diluer le béton, ce qui prend beaucoup moins de place que dans les solutions qui fonctionnent avec des bassins de décantation. »
Chryso : Un additif spécial retours de béton
![Chryso va mettre sur le marché un adjuvant permettant de neutraliser l’action du ciment dans les résidus de béton présent dans la toupie. [©ACPresse]](https://www.acpresse.fr/wp-content/uploads/2020/10/11-Recyclage-Chryso-600x400.jpg)
Chryso va mettre sur le marché un adjuvant permettant de neutraliser l’action du ciment dans les résidus de béton présent dans la toupie.
[©ACPresse]
Avec son offre d’adjuvants et de service Quad, dédiés aux granulats complexes, Chryso propose déjà des solutions pour l’utilisation des granulats issus de la déconstruction. Au printemps prochain, l’industriel proposera une solution de traitement des retours béton immédiatement sur le site de production. Cette technologie va permettre de neutraliser l’action du ciment, en empêchant les granulats de se réagglomérer. « L’additif mis au point permet, en sortie de toupie, d’obtenir une grave, reprenable à la chargeuse, transportable comme un granulat classique et réutilisable dans des formulations bétons, mais en dehors du champ de ma norme béton NF EN 206/CN. Mais aussi dans la construction comme remblais, comme sous-couche routière ou encore comme béton de propreté, résume Marc Plancon, directeur adjoint de la BU Béton chez Chryso. C’est une solution destinée aux clients, qui souhaitent valoriser leurs déchets et optimiser leur filière de recyclage. »
Unibéton : Une politique anti-gaspi
![Chez Unibéton, environ 10 % de ses installations possèdent des équipements de lavage et de valorisation des granulats, le reste dispose de bennes de durcissement. [©ACPresse]](https://www.acpresse.fr/wp-content/uploads/2020/10/12-Recyclage-Unibeton-600x400.jpg)
Chez Unibéton, environ 10 % de ses installations possèdent des équipements de lavage et de valorisation des granulats, le reste dispose de bennes de durcissement.
[©ACPresse]
Unibéton produit pas moins de 4 Mm3/an de béton. De manière progressive, il a équipé la totalité de ses quelque 200 centrales de dispositifs de récupération et de traitement des résidus de béton. Ceci, pour en faire des granulats dits “récupérés”. Environ 10 % de ses installations possèdent des équipements de lavage et de valorisation des granulats, le reste disposant de bennes de durcissement. Si le pourcentage de retours de béton frais atteint en centrale la moyenne nationale de 3 %, Unibéton a décidé de facturer à ses clients le traitement de leurs résidus pour limiter le gaspillage. « Nous ne refacturons pas le matériau, mais le traitement de retour de ce rebus, précise Vincent Waller, directeur qualité chez Unibéton. Le chantier va donc payer deux fois. Une première fois, parce qu’il commande trop de béton qu’il n’utilise pas de manière complète. Et une seconde fois, parce qu’il retourne à la centrale l’excédent. »
Retrouvez cet article dans le n° 948 de Process Industriels, supplément de Béton[s] le Magazine n° 87